Mixing Equipment for Plastics and Composites
Schold provides industrial mixing equipment for plastics and composites as a trusted partner in the industry. Our specialized dispersers, mixers, and mills achieve precise dispersion and thorough mixing of polymers and additives, ensuring high-quality formulations. From small, lab-sized batches to large, production-sized volumes, Schold has an equipment solution.
Mixing Equipment for Plastics and Composites
Schold provides industrial mixing equipment for plastics and composites as a trusted partner in the industry. Our specialized dispersers, mixers, and mills achieve precise dispersion and thorough mixing of polymers and additives, ensuring high-quality formulations. From small, lab-sized batches to large, production-sized volumes, Schold has an equipment solution.
Recommended Mixing Equipment
Find common base models/designs of mixing equipment for plastics and composites. Questions? Need a quote? Schold can assist with questions or customized options specific for your application.
TRUSTED COMPANIES USING SCHOLD MIXING EQUIPMENT FOR PLASTICS AND COMPOSITES:
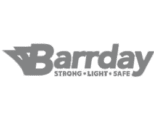
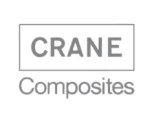
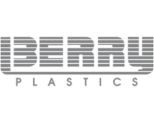
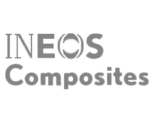
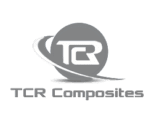
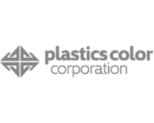
Product Applications
Plastics and composites are used in many areas and require specific properties and performance. Our team of experts work with many companies in this space, and Schold equipment is custom designed to process these applications (along with many others):
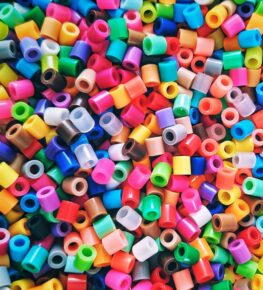
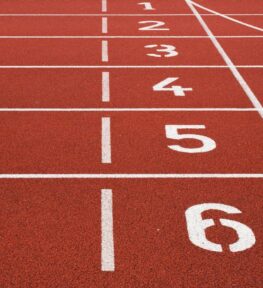
- Polymer Blending: Achieving uniform blending of polymers, additives, and reinforcing agents to ensure consistent material properties in the final product. (See Low-Speed Mixer).
- Composite Formulation: Developing and refining formulations for composite materials by dispersing reinforcing fibers, fillers, and additives uniformly for enhanced strength and performance.
- Resin Mixing: Homogenizing resin blends with additives to create customized formulations with specific characteristics for applications such as molding and extrusion. (See Rotor Stator Mixer).
- Colorant Dispersion: Ensuring even dispersion of pigments and colorants in plastic formulations to achieve desired color consistency and appearance in the final product. (See High-Speed Disperser).
- Adhesive and Sealant Production: Formulating and blending adhesives and sealants with precise dispersion for applications in bonding and sealing various plastic and composite components.
- Polymer Melt Processing: Processing polymer melts with additives and modifiers to achieve desired properties before shaping through molding or extrusion processes.
- Composite Resin Impregnation: Impregnating reinforcing fibers with resin matrices to create composite materials with optimized strength, durability, and dimensional stability.
- Polymer Recycling: Breaking down and dispersing recycled polymers for reuse in manufacturing processes, contributing to sustainable practices in the industry.
- Additive Manufacturing (3D Printing): Preparing and dispersing polymer-based materials with additives for use in additive manufacturing processes, such as 3D printing.
- Filler Dispersion: Achieving uniform dispersion of fillers, such as glass or carbon fibers, within polymer matrices to enhance mechanical properties in composite materials.
- Thermoset Resin Curing: Facilitating the curing process of thermoset resins by proper mixing and dispersion of curing agents, ensuring the desired material properties.
- Nano-Particle Dispersion: Dispersing nanomaterials within polymer matrices to incorporate advanced properties, such as improved strength, conductivity, or flame resistance. (See Lab Bead Mills from EMI Mills Division).
- Polymer Coating Production: Preparing and dispersing coatings for application on plastic or composite surfaces to enhance properties like durability, adhesion, and corrosion resistance.
Mixing/Processing Challenges
Plastics and composites manufacturers run in to range of challenges including polymer homogenization, particle size control, and more. Whether you choose Schold or another partner, selecting the proper industrial mixing equipment for plastics and composites is crucial for overcoming these common issues:
- Polymer Homogenization: Achieving consistent blending and homogenization of polymers is critical. This ensures uniform material properties, which is required for producing materials with predictable characteristics and integrity.
- Particle Size Control: Precise control over particle size distribution during milling is essential for tailoring mechanical and thermal properties in plastics and composites. This involves attention to the size/distribution of particles to meet specific requirements. (See Media/Bead Mills).
- Additive Dispersal: Achieving even dispersion of additives is a crucial step to enhance the overall product performance and characteristics. This involves uniformly incorporating additives throughout the material matrix to achieve the desired properties.
- Temperature Control: Addressing temperature-related challenges prevents overheating or degradation of thermally sensitive materials during processing. Maintaining optimal temperature ensures proper integrity and properties of the product. (See the Vacuum Drum Mixer).
- Scale-Up Challenges: Adapting for larger production while maintaining precision is essential for meeting growing demand. Scaling involves addressing logistical, operational, and efficiency challenges to ensure consistent product quality. Schold can assist with this.
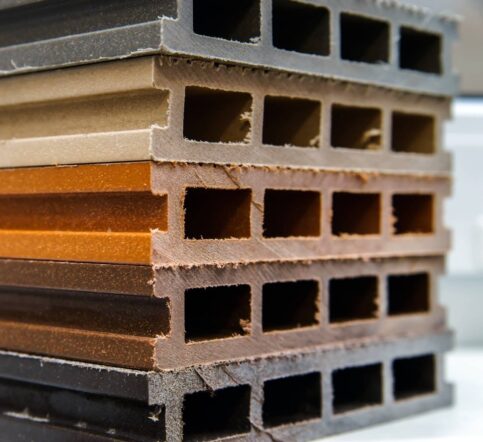
- Polymer Homogenization: Achieving consistent blending and homogenization of polymers is critical. This ensures uniform material properties, which is required for producing materials with predictable characteristics and integrity.
- Particle Size Control: Precise control over particle size distribution during milling is essential for tailoring mechanical and thermal properties in plastics and composites. This involves attention to the size/distribution of particles to meet specific requirements. (See Media/Bead Mills).
- Additive Dispersal: Achieving even dispersion of additives is a crucial step to enhance the overall product performance and characteristics. This involves uniformly incorporating additives throughout the material matrix to achieve the desired properties.
- Temperature Control: Addressing temperature-related challenges prevents overheating or degradation of thermally sensitive materials during processing. Maintaining optimal temperature ensures proper integrity and properties of the product. (See the Vacuum Drum Mixer).
- Scale-Up Challenges: Adapting for larger production while maintaining precision is essential for meeting growing demand. Scaling involves addressing logistical, operational, and efficiency challenges to ensure consistent product quality. Schold can assist with this.